Mit dem Kommunikationsstandard OPC UA soll die vernetzte Produktion auch für die industrielle Bildverarbeitung möglich werden. Was genau dahintersteckt und welche Vorteile OPC UA für Vision und Automatisierung mit sich bringt, schauen wir uns in diesem Beitrag genauer an.
Auch wenn es bereits länger her ist: Erinnern Sie sich noch an Ihren letzten Urlaub in einem exotischen Land? Höchstwahrscheinlich haben Sie die Landessprache nicht gesprochen und haben damit gehadert, sich verständlich zu machen. Eine anstrengende und frustrierende Angelegenheit!
Ähnlich ergeht es der industriellen Bildverarbeitung, Maschinen und Anwendungen der Industrie 4.0. Es gibt unzählige herstellerspezifische Kommunikationsprotokolle mit jeweils individuellen Eigenschaften.
Einheitlicher Kommunikationsstandard über OPC UA
Doch wo wir Englisch lernen, um uns nahezu überall auf der Welt verständigen zu können, fehlte den Produktionsanlagen lange eine gemeinsame Sprache. Dementsprechend war die frühe Industrie 4.0 auf Dolmetscher angewiesen, die sich jeweils umständlich in eine andere Sprache einarbeiten mussten. Kam ein drittes Kommunikationsprogramm hinzu, fing die gesamte Arbeit von vorne an – mit dem zusätzlichen Nachteil, dass sich der Übersetzungsaufwand nun verdoppelte oder wichtige Informationen durch eine zweifache Datenübersetzung verloren gingen.
Keine gute Ausgangslage für die vernetzte und automatisierte Produktion der Industrie 4.0. Und schon gar nicht für die industrielle Bildverarbeitung – schließlich wird sie in den meisten Anwendungsfällen als Unterstützung für Roboter und Anlagen eingesetzt und muss entsprechend umfangreiche Informationen weitergeben. Mangelnde Effizienz und komplexe, individuelle Datenlösungen verschlimmerten die Situation zusätzlich.
Es überrascht daher nicht, dass bereits in den frühen 2000ern Überlegungen angestellt wurden, diesen Missstand zu beheben. So stellte die OPC Foundation bereits im Herbst 2006 die erste Version seines neuen offenen Kommunikationsstandards OPC UA (Open Platform Communications Unified Architecture) vor.
OPC als Grundlage der Industrie 4.0
Die Einführung dieses neuen Kommunikationsprotokolls kam dabei einem Paukenschlag in der Industrie gleich: OPC UA ist nicht nur in der Lage, die Kommunikation in einer vernetzten Produktion schnell, einfach und zuverlässig zu sichern, sondern gleichzeitig auch maschinenlesbare semantische Beschreibungen der transportierten Informationen zu liefern.
Echtzeit-Datenübertragung
Damit schuf das Konsortium eine wichtige Grundlage, um in den kommenden Jahren die vernetzte Produktion Wirklichkeit werden zu lassen. Denn OPC UA kann in der Fertigung über alle Datenebenen hinweg in Echtzeit eingesetzt werden. Das ermöglicht die Kommunikation auf Ethernet-Basis – eine oftmals sogar bereits vorhandene Infrastruktur.
Zusätzlich arbeitet OPC UA vollkommen herstellerunabhängig und plattformneutral. Die Daten lassen sich auch aufgrund der maschinenlesbaren semantischen Beschreibungen jederzeit eindeutig interpretieren. Daten können nicht zum falschen Zeitpunkt oder vom falschen Agenten ausgelesen werden. Damit eröffnet der Kommunikationsstandard Unternehmen zusätzliche Spielräume bei der Ausgestaltung ihrer Produktionshallen.
Security by Design
Weiterhin setzt die Kommunikations- und Informationsschicht nativ auf Datensicherheit. In Zeiten digitaler Erpressungsversuche eine wichtige Grundvoraussetzung. Ebenfalls relevant: Informationen werden dank Datentransports mithilfe des TCP/IP Protokolls zuverlässig transportiert – und das bei minimaler Bandbreite. Das System verschlüsselt, signiert und authentifiziert übertragene Daten automatisch. Auch Störeinflüsse oder kurze Bandbreitenausfälle können OPC UA nichts anhaben, denn es puffert Daten für diesen Fall.
War der Einsatz von Feldbussen zuvor in der Fertigungsindustrie Standard, übernimmt nun OPC UA. Und das zu Recht: Zwar gelten auch Feldbusse als „standardisiert“, doch laut IEC 61 158 gibt es 19 verschiedene Feldbus-Standards – die alle inkompatibel zueinander sind. OPC UA hingegen ist untereinander vollkommen kompatibel. Häufigste Konfiguration ist hier die Client-/Server-Kommunikation. Dabei sendet jeder Client (z.B. Roboter) eine Anfrage an den OPC UA-Server und erhält auch direkt von diesem eine Antwort. Um diese Verbindung sicherzustellen, verfügt OPC UA über einen „Heartbeat“ – eine dauerhafte Verbindungsüberwachung.
Die Vorteile von OPC UA lassen sich direkt in die Bildverarbeitung übertragen
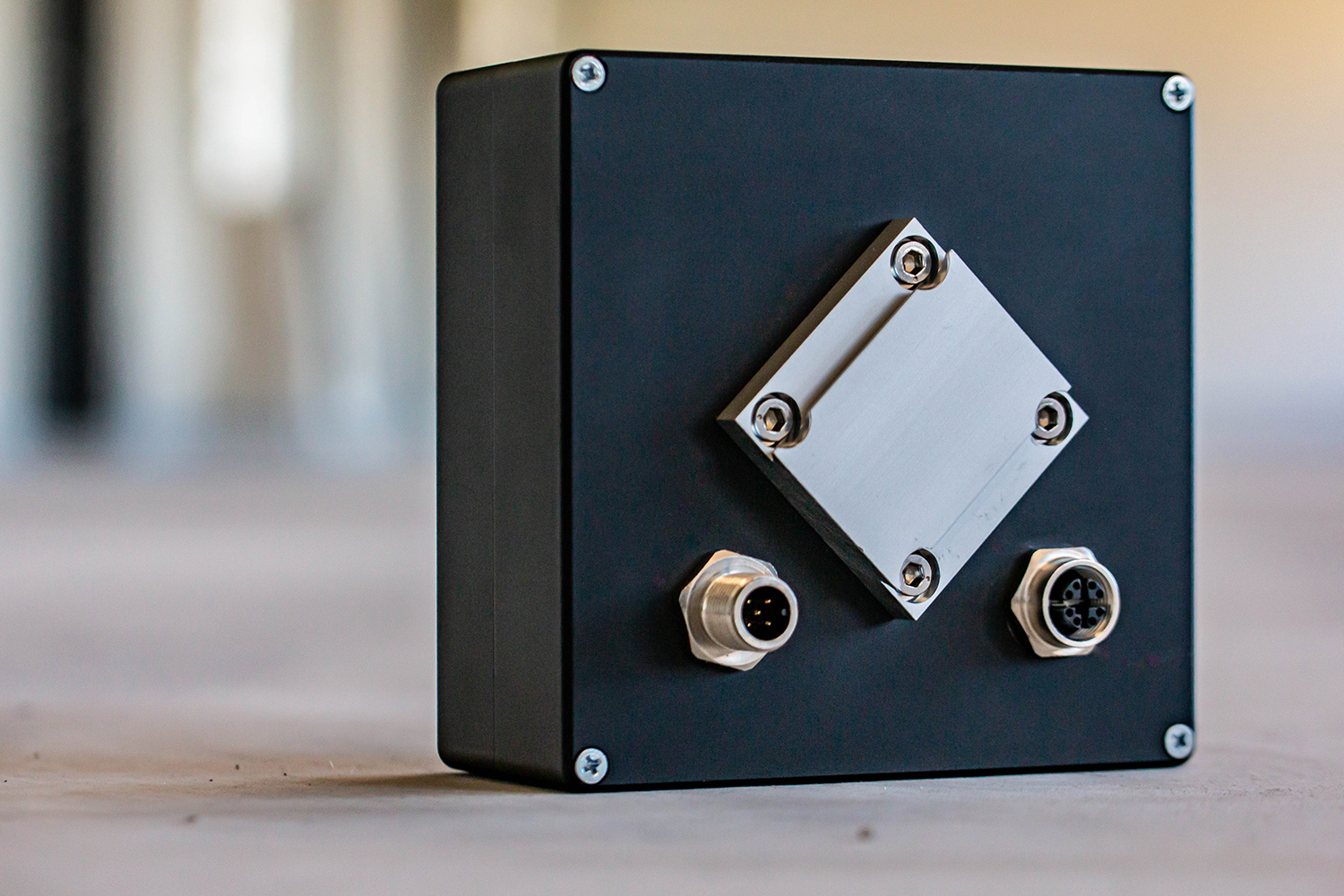
Anschlüsse des kompakten 3D-Vision-Sensors LumiScanX – Dank Ethernet-Anschluss problemlos in OPC UA integrierbar
All diese Vorteile führen dazu, dass auch die industrielle Bildverarbeitung großes Interesse an OPC UA gefunden hat. Eine zuverlässige, schnelle Datenübertragung ohne Informationsverlust stellt für zeitkritische Vision-Anwendungen einen großen Gewinn dar. Der offene Kommunikationsstandard kann dementsprechend auch über die gesamte Bandbreite der Bildverarbeitungsaufgaben eingesetzt werden:
- Konfiguration
- Controlling
- Kommunikation mit weiteren Maschinen und Robotern
Damit bietet OPC UA mehr Unternehmen einen einfachen Zugang zu Machine Vision, ohne einen neuen Datenstandard in ihre Peripherie einfügen zu müssen. Der Umgang mit einem bereits bekannten Kommunikationsstandard kann außerdem helfen, Einstiegshürden zu senken und kritische Wissenslücken zu vermeiden.
Um diese Chancen vollends zu nutzen und OPC UA optimal auf die Anforderungen der industriellen Bildverarbeitung anzupassen, entwickelt die OPC Foundation gemeinsam mit dem VDMA den Standard weiter. So ist in der VDMA-Spezifikation VDMA 401100-1 OPC UA for Machine Vision bereits heute ein standardisiertes Informationsmodell festgehalten. Damit sollen sich die individuellen Vision-Anforderungen leicht verständlich umsetzen lassen und das gesamte Spektrum der Bildverarbeitung abdecken.
OPC UA – Meilenstein für die vernetzte Bildverarbeitung
Die Nutzung von OPC UA stellt daher einen wichtigen Meilenstein für eine intuitiv nutzbare Bildverarbeitung dar – quasi die Einführung des Englischen als internationaler Businesssprache.